Resumen de la aplicación:
Las nuevas tecnologías y características están trayendo nuevos desafíos al diseño de aplicaciones automotrices. Esto hace que las pruebas rigurosas de durabilidad y fatiga sean aún más cruciales. Las pruebas de durabilidad automotriz respaldan la evaluación de vehículos, subsistemas y componentes de los fabricantes de componentes y OEM para determinar la vida útil esperada del producto.
Las pruebas usan movimientos y fuerzas del mundo real para evaluar y validar el diseño y mejorar la calidad. FUTEK apoya a los OEM automotrices y a los fabricantes de subsistemas al ofrecer una amplia gama de sensores optimizados para pruebas automotrices (sensores de automóviles). Además de los vehículos completos, las pruebas de durabilidad automotriz evalúan componentes que incluyen el motor, la suspensión, la palanca de cambios, los frenos, el volante, las ventanas, el chasis, el marco, el sistema de infoentretenimiento, las bisagras de las puertas y los asientos, los interiores y la suspensión. Las capacidades incluyen pruebas de fatiga cíclica, seguridad funcional, deflexión, vibración electrodinámica, mediciones de tensión y más.
Capacidades de prueba automotriz de los sensores FUTEK
- Prueba de Durabilidad y Rendimiento;
- Prueba de Fatiga y Vibración;
- Ensayos de Torsión y Rotación;
- Prueba de durabilidad multieje;
- Seguridad funcional;
- Validación de lazo de control electromecánico.
-
FMVSS 118: Sistemas de ventanas, divisiones y paneles de techo accionados eléctricamente;
ASTM D3574 B1 / ISO 2439: Deflexión de la fuerza de indentación de la espuma del asiento (IFD);
SAE J2909: Procedimiento de prueba de distancia de frenado en seco y húmedo para vehículos ligeros (prueba de frenos);
ECE R13H: Disposiciones para el frenado de turismos;
ISO 7975: Automóviles de pasajeros - Frenado en un giro - Método de prueba de bucle abierto;
ISO 13849-1:2015 Seguridad de la maquinaria - Partes de los sistemas de control relacionadas con la seguridad;
ISO 26262-1:2018 Vehículos de carretera - Seguridad funcional
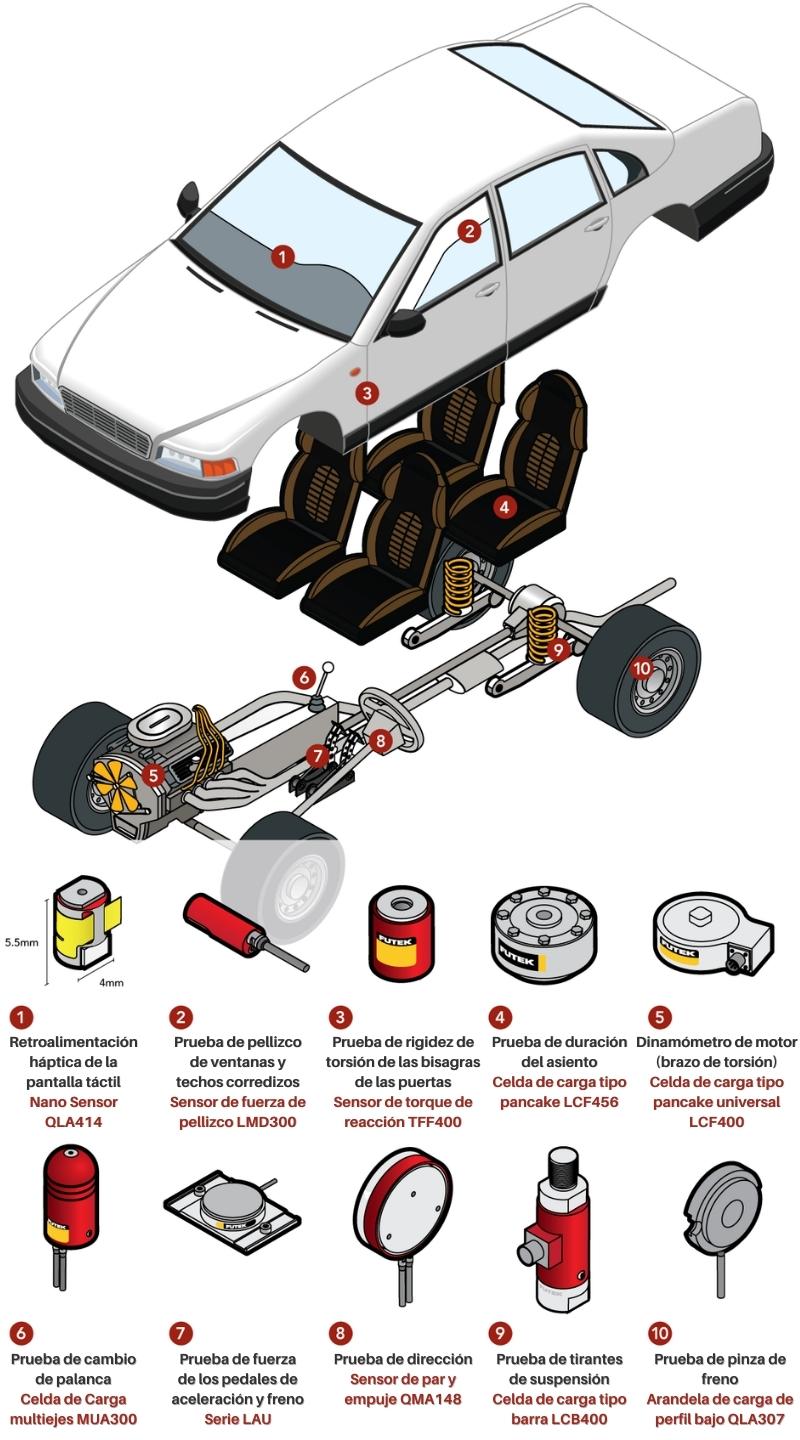
Cómo funciona:
- Retroalimentación de pantalla táctil: Al incorporar celdas de carga para medir la fuerza de contacto, la computadora a bordo del auto puede confirmar entradas correctas de comandos sobre la pantalla.
- Presión sobre ventanas y techo del auto: Al utilizar la celda de carga para pellizco, los fabricantes de automóviles pueden verificar la fuerza que resisten las ventanas y el techo del automóvil. También se aseguran de que el producto pueda cumplir los ciclos de vida que se calcularon en diseño.
- Dureza torsional de las bisagras automotrices: Cuando hablamos de bisagras, el torque que se requiere para abrir o cerrar la puerta o panel, es esencial. La energía requerida depende del peso de la puerta, el arco de distancia que recorre la puerta y la posición de las bisagras.
- Durabilidad del asiento: En la industria automotriz ya existen robots que se utilizan para hacer ciclos de prueba en los materiales del asiento. Se prueba con condiciones que emulan a personas de todas edades y tamaños. Para esto puede utilizarse una celda de carga tipo panqueque, colocarla en el asiento y hacer pruebas de durabilidad.
- Dinamómetro de motor: Los ingenieros de manufactura utilizan dinamómetros para medir la salida de potencia y con ello medir factores de rendimiento como caballos de fuerza, aceleración y kilometraje.
- Prueba de palanca de cambios: el sensor de palanca de cambios MAU300 es otro producto único diseñado para la industria automotriz y es ideal para aplicaciones de medición de la fuerza de accionamiento de palancas de cambios en automóviles. Diseñado para probar las cargas Fx y Fy que tienen lugar durante el cambio de marchas, el MAU300 está diseñado para uso manual/pruebas en humanos.
- Aceleración y fuerza de los pedales de freno: La prueba del sistema de frenos normalmente se lleva a cabo durante varias etapas del proceso de fabricación. Comienza en la etapa de desarrollo inicial, seguida de pruebas de resistencia, laboratorio y pista, y continúa a través del proceso de producción para garantizar la calidad adicional. Utilizando sensores de fuerza de pedal LAU220 (también conocidos como celda de carga de freno), los fabricantes de automóviles pueden verificar la seguridad y confiabilidad de la mecánica de frenado de su automóvil. Los sensores de fuerza del pedal (sensores del vehículo) están diseñados para medir la carga aplicada a los pedales de freno, acelerador y embrague durante la aceleración, desaceleración y cambios de transmisión.
- Volante: la tecnología Steer-by-Wire (SbW) en la industria automotriz es el uso de dispositivos electrónicos, actuadores y algoritmos para reemplazar las conexiones hidráulicas y mecánicas entre el volante manual y la carretera. Durante la fase de validación del producto, el sensor de empuje y torsión de bajo perfil QMA148 proporciona a los ingenieros de control y control de calidad las herramientas adecuadas para medir la torsión rotacional aplicada a los controles de dirección.
- Tirante de suspensión - Pruebas de fatiga y durabilidad del marco de la suspensión delantera: Los complejos sistemas de suspensión multipunto que se utilizan en vehículos de alto rendimiento requieren el uso de modelos y simulaciones para garantizar el cumplimiento bajo carga. Sin embargo, el paso final para validar el modelo de simulación de pruebas en vivo. Para lograr esto, las celdas de carga se colocan en línea con cada brazo de suspensión, lo que proporciona datos de la carga que pasa por cada brazo, mediciones precisas de la carga de la dirección y agarre indirecto de los neumáticos delanteros que permite ajustar el sistema de suspensión para optimizar el rendimiento y el manejo.
- Pinza de freno: en los sistemas de freno por cable, los controladores centrales requieren información precisa sobre la fuerza de sujeción entre la pastilla de freno y el disco en función del desplazamiento de la pastilla, que normalmente se indica como la curva característica de la pinza. Debido al envejecimiento, la temperatura y otras variaciones ambientales, las curvas características del calibre varían con el tiempo. Por lo tanto, la calibración automática de la pinza en tiempo real es vital para una acción de frenado de alto rendimiento y la seguridad del vehículo. Además, durante la validación del diseño, los ingenieros utilizan un sistema de medición de fuerza para validar y calibrar los sistemas de bucle cerrado de freno por cable. La celda de carga tipo arandela QLA307 tiene un perfil bajo y puede soportar cargas masivas, y se usa comúnmente para la celda de carga Caliper para la prueba de pastillas de freno.
Productos en uso:
- QLA414 Nano Sensor – Retroalimentación de pantalla táctil;
- LMD300 Sensor de fuerza para pellizco – Prueba de pellizco para ventana y techo;
- TFF400 Sensor de torque a reacción – Dureza en el movimiento de bisagras para puerta de auto;
- LCF456 Celda de carga tipo panqueque – Pruebas de durabilidad de asiento;
- LCF400 Celda de carga tipo panqueque universal – Dinamómetro de motor;
- MAU300 Sensor multiaxial – Dureza de la palanca de cambio;
- LAU220 Sensor de fuerza de pedal – Fuerza en pedales de aceleración y freno;
- QMA148 Sensor de torque y empuje – Pruebas de volante;
- LCB400 Celda de carga tipo barra – Prueba de suspensión;
- QLA307 Celda de carga tipo arandela – Prueba de pinzas para freno.